

From ancient Nabataean concrete to modern-day skyscrapers, our urban landscape has grown into a concrete jungle. Yet this growth has come at a cost — cement production accounts for 7% of global CO₂ emissions. Today, the Sultanate of Oman is leading a transformation towards sustainable construction with innovative solutions like calcined clay.
We have come far from the earliest recordings of concrete structures back in 6500 BC by the Nabataea traders in regions of Syria and Jordan. Today, we’ve now covered 1.18 million km2 of the earth with concrete, asphalt and other types of man-made surfaces.
But this is not how we intend to carry on. With self-awareness comes change. The Global Cement and Concrete Association stated that cement production around the world accounts for approximately 7% of global CO₂ emissions (2021). Today, we understand the impact of concrete on our CO₂ emissions and we know that it is time to change the way we build our world, one brick at a time.
We have started to tackle these emissions on all fronts, and this includes turning our concrete jungle around with alternative, more sustainable solutions — this is where calcined clay comes in.
Emerging as a promising alternative to traditional cement, it has the ability to significantly reduce CO₂ emissions whilst also maintaining essential characteristics of the Portland cement that we know so well, from its strength, durability and workability to its versatility, affordability and sustainability; making a viable and scalable solution to tackle our net-zero targets in the construction sector on a global scale.
Oman’s advancements in its sustainability goals include innovative solutions such as calcined clay in the construction sector. Calcined clay brings less CO₂emissions to the table with lower processing temperatures (700 - 850°C as opposed to 1,400 –1,500°C) than cement, due to using less of cements’ pebble-like ‘clinker’ material that requires heating in higher temperatures. To make it clearer — clinker is responsible for about 90% of the CO₂ emissions in cement manufacturing. As noted by the International Energy Agency (IEA); the clinker-to-cement ratio significantly influences the carbon intensity of cement production.
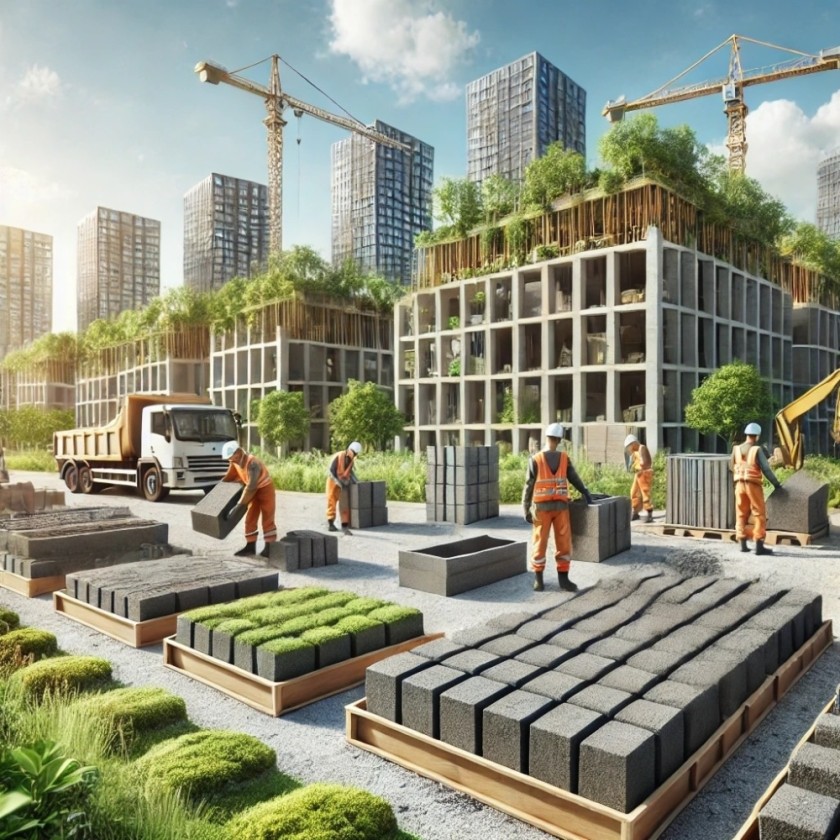
Calcined clay, on the other hand, is produced by heating kaolinite-rich clays at its relatively low temperatures. The process requires significantly less energy compared to cement clinker production, making it an environmentally friendly alternative and aligning with Oman’s objectives of reducing emissions, promoting a circular economy and conserving natural resources.
In a significant initiative towards sustainable construction efforts in Oman, the establishment of a calcined clay factory is set to commence initial production operations in the first quarter of 2025, developed by the Middle East Calcined Clay Company in collaboration with Oman’s Public Establishment for Industrial Estates (Madayn) in Suhar Industrial City. The factory will be dedicated to reviving the production of the Omani “Sarooj” cement alternative, a type of calcined clay historically utilised for constructing forts and hydraulic installations.
It will feature two production lines with a combined annual capacity of approximately 250,000 tonnes, incorporating energy-saving technologies and automated production processes including a modern laboratory for sample testing and quality control.
The facility, set to occupy 45,000 square metres, has an investment of RO 5.4 million — with aims to support local production and reduce reliance on imported materials. The state-of-the-art facility will play a crucial role in integrating calcined clay into concrete suited for Oman’s climate with advantages of durability and resistance to water permeability.
The combined impact of calcined clay adoption leaves Oman on track to achieving up to a 40% reduction in cement usage; cutting carbon dioxide emissions significantly. These efforts also enhance infrastructure durability, reduce maintenance costs and create local economic opportunities — not only addressing immediate environmental challenges but also establishing a foundation for long-term sustainability.
Calcined clay is at the heart of our transformation to low-carbon alternatives to traditional cement. Produced by heating kaolinite-rich clays at lower temperatures than those required for cement clinker production; reducing energy consumption and carbon emissions while improving the durability and chemical resistance of concrete. Global players like Econiclay are unlocking the full potential of clay-based materials. Specialising in integrating calcined clay into low-carbon concrete solutions, it helps construction projects achieve reductions in CO2 emissions without compromising performance. With a focus on tailoring clay mixes to regional climates that makes its solutions particularly relevant for Oman’s environment. By leveraging its expertise, Econiclay enables developers to meet sustainability certifications such as LEED and BREEAM; aligning with Oman’s focus on green building practices.
By incorporating calcined clay, Oman is reducing its reliance on cement, significantly cutting carbon emissions, not only addressing immediate environmental challenges but also building a resilient and sustainable legacy for future generations.
Oman Observer is now on the WhatsApp channel. Click here